Understanding Metal Rollforming Systems: Types, Uses, and Advantages
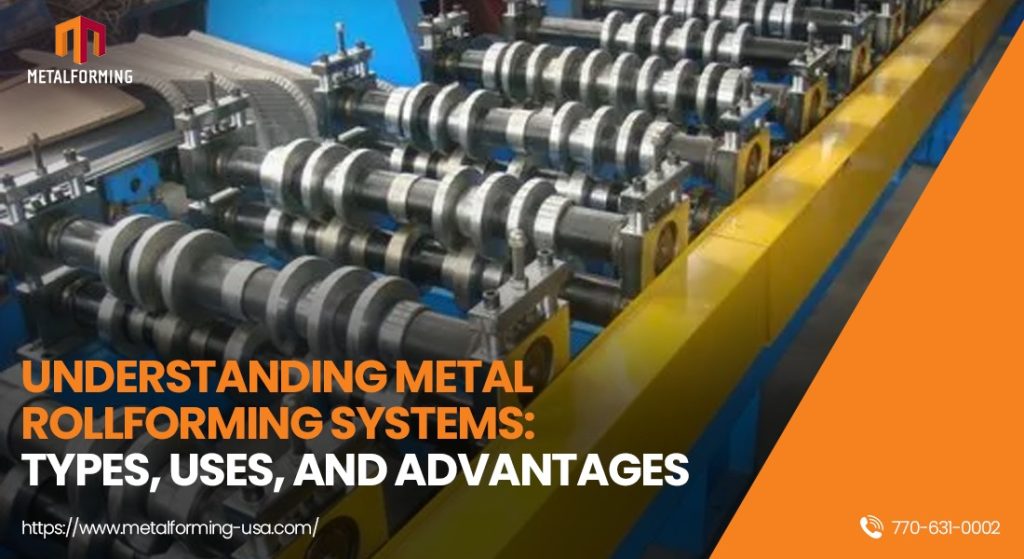
Metal rollforming systems represent a cornerstone in the manufacturing sector, especially in industries where precision and efficiency in metal shaping are paramount. These systems facilitate the transformation of metal sheets into specific profiles through a series of rollers, each meticulously designed to incrementally bend the metal into the desired shape. This article delves into the intricacies of metal rollforming systems, exploring their types, uses, and the significant advantages they offer over traditional metal forming methods.
Table of Contents
Selecting the Best Metal Rollforming System for Your Needs
Choosing the ideal metal rollforming system for your project or production line is a decision that hinges on a comprehensive understanding of your unique requirements. The selection process is influenced by a variety of critical factors, including the type of metal you’re working with, the intricacy of the profiles needed, and the anticipated production volume. Below is a step-by-step guide to help you select the best metal rollforming system tailored to your project’s specific requirements:
- Assess Metal Type and Thickness: Begin by identifying the type of metal and its thickness. This step is crucial as different systems are optimized for various metal types and thickness ranges, impacting the system’s compatibility with your material.
- Define Profile Complexity: Consider the complexity of the profiles you intend to produce. Systems vary in their capabilities to handle simple to highly complex profiles, influencing the precision and quality of the final product.
- Determine Production Volume: Estimate the volume of production to ensure the selected system can efficiently meet your output requirements without compromising on quality.
- Consider Structural Requirements: For projects involving construction or other industries where structural integrity is paramount, select a system that not only achieves precise dimensions but also maintains the metal’s structural strength.
- Evaluate Adaptability for Custom Profiles: If your project demands unique profiles, opt for a system or custom rollforming services that offer flexibility and quick adaptability to change setups according to specific profile requirements.
- Analyze System Versatility: Look for systems that provide versatility to accommodate a wide range of applications. This ensures that the equipment can be utilized for various projects, maximizing your investment.
- Review Advanced Design and Technology Features: Investigate the design and technological advancements incorporated into the system. Features such as automated controls, inline processing capabilities, and real-time adjustments can significantly enhance efficiency and product quality.
By methodically assessing these aspects, you can make an informed decision on the most suitable metal rollforming system that aligns with the specific needs of your project or production line. The right system not only ensures the production of high-quality profiles but also contributes to the overall efficiency and success of your manufacturing operations.
Maximizing Productivity with Advanced Rollforming Techniques
When it comes to metal fabrication, advanced rollforming techniques stand at the forefront of innovation, driving productivity to unprecedented levels. These techniques leverage cutting-edge technology and automation to refine and accelerate the rollforming process, ensuring manufacturers can meet the demands of precision, efficiency, and scalability. Below, we delve into the key advanced rollforming techniques that are reshaping the industry, each characterized by its unique contribution to enhancing the production line:
- Computerized Control Systems: These systems represent the nerve center of modern rollforming lines, providing precise control over roller movements and adjustments. By minimizing manual intervention, they ensure each piece of metal is formed with unparalleled accuracy, significantly reducing material waste and enhancing production speed.
- Automated Material Handling: This technique involves the use of robotics and conveyor systems to automate the movement of materials through the rollforming process. From feeding the metal sheets into the rollers to transporting the finished profiles for further processing, automated material handling streamlines operations, reducing labor costs and minimizing the risk of errors.
- Inline Punching and Cutting Processes: Traditionally separate operations, punching and cutting are integrated directly into the rollforming line. This allows for the creation of holes, notches, and end cuts in profiles without halting the rollforming process. The result is a seamless production flow that eliminates the need for post-rollforming secondary operations, saving both time and resources.
- Integration of Additional Fabrication Processes: Advanced rollforming systems are now capable of incorporating other metal fabrication processes, such as welding or embossing, into the rollforming line. This integration facilitates the production of more complex profiles in a single pass, enhancing the system’s versatility and the value of the final product.
- Precision Roller Adjustments: The latest rollforming machines feature sophisticated mechanisms for adjusting roller positions with extreme precision. This allows for quick changes between different profile designs and ensures that each profile maintains strict adherence to dimensional tolerances, crucial for high-quality production.
- Real-time Monitoring and Feedback: Equipped with sensors and diagnostic tools, modern rollforming lines offer real-time monitoring of the rollforming process. This capability allows for immediate adjustments based on feedback, ensuring consistent quality and minimizing downtime due to errors or malfunctions.
Conclusion
Metal rollforming systems play an indispensable role in modern manufacturing, offering a combination of precision, efficiency, and versatility that is hard to match with other metal forming methods. Whether it’s for large-scale production in the construction industry or for custom profiles required in specialized projects, these systems provide a reliable solution.
By understanding the features and benefits of metal rollforming, as well as the rollforming machine maintenance and technological advancements associated with these systems, manufacturers can make informed decisions to optimize their production lines, ensuring high-quality outcomes and maximized productivity.
Frequently Asked Questions
How do metal rollforming systems differ from other metal shaping processes?
Metal rollforming systems progressively bend metal strips into desired profiles through a series of rollers, unlike other processes that cut, press, or extrude metal into shape, offering continuous operation and efficiency for long, uniform sections.
What factors should I consider when purchasing a rollforming system?
When purchasing a rollforming system, consider the metal types and thicknesses it can handle, the complexity of profiles needed, production volume capabilities, system adaptability for various projects, and the availability of advanced features for efficiency and precision
Can rollforming systems be customized for specific project needs?
Yes, rollforming systems can be customized to meet specific project needs. Customization options include adapting roller designs, integrating additional processes like punching or cutting, and configuring the system for unique metal types and profile complexities to achieve precise results.