Practical Tips to Enhance Safety in a Chemical Handling Industry
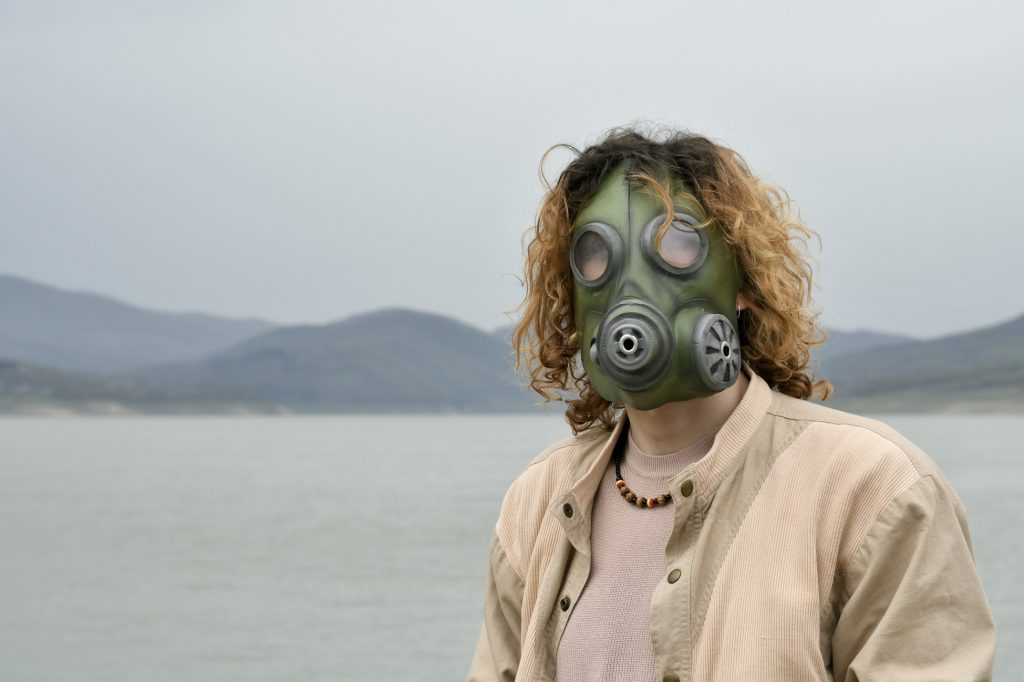
Safety is one of the primary concerns for people working in chemical industries. Although nobody wants to get hurt, some people neglect relevant safety measures because of the extra time and effort required to avoid injuries. Paying attention to workplace safety is the first step toward preventing work-related injuries and diseases. Therefore, employees and supervisors should make the environment safe and minimize health hazards. Improved workplace safety also helps employers reduce compensation claims and minimize workers’ sick days. This article will discuss tips to enhance safety in chemical industries.
Table of Contents
Ask Employees to Report Unsafe Situations
Some employees fear their supervisors or employer and might not report certain conditions they feel might lead to injuries or diseases. However, supervisors should encourage employees to report potentially dangerous situations such as broken floor tiles, faulty safety gear, dirty surfaces, broken objects, or unreliable safety equipment. Besides, the employees should also try to enhance safety by removing things that could hurt others from the workplace. Addressing these issues immediately minimizes the chances of accidents in the chemical industry.
Ensure Employees Use Relevant Safety Equipment
Personal protective equipment can help minimize accidental injuries and illnesses in a chemical factory. Therefore, the management should provide safety equipment and ensure the workers use it appropriately. The safety equipment every worker should have in a chemical factory includes protective footwear, a mira filter, an apron, gloves, a face shield, an overall, and chemical-resistant glasses. Supervisors should encourage workers to use PPE appropriately in areas prone to chemicals. Employees should know where the PPEs are stored and how to inspect them for signs of wear. Compromised safety equipment should be discarded and replaced immediately to avoid compromising safety.
Install Emergency Equipment
Buildings that store or handle hazardous chemicals should have relevant emergency equipment to minimize the chances of injury. For example, if an employee accidentally splashes chemicals into their eyes, an emergency eyewash could prevent blindness. Flammable chemicals might cause fire, but fire extinguishers can help control the situation. Therefore, supervisors should ensure the workplace is equipped with firefighting equipment and trained firefighters. Always hire experts to test the equipment regularly and ensure it doesn’t fail during an emergency.
Train Employees About Safety
Some employees may expose themselves or their colleagues because they do not understand the risks in a chemical factory. Besides, jargon that employees use in the chemical industry may confuse new employees or those recently transferred from other departments. Since confusion could lead to accidents, supervisors should train new workers about safety to eliminate confusion. Besides understanding the jargon, employees must know how to respond to emergencies and where they should run for safety.
Provide a Clean and Safe Location for Food or Drinks
Some chemicals can lead to health problems when ingested. Therefore, every chemical factory should have a designated area for eating and drinking. If the employees are allowed to walk around eating and drinking, they might consume contaminated food or drink. The ideal area for food and drinks should be away from the worksite and chemical storage section. It should have sinks, clean water, and hand-washing soaps to ensure employees clean their hands and faces before eating. The management should also have policies preventing workers from entering the food area with chemicals or entering the workplace with food to prevent cross-contamination.
Prevent Slips and Trips
Slip or trip and fall accidents are common in factories, and there is a need to minimize the risks. Each chemical factory should have trained cleaners to deal with chemical spills and place relevant warning signs. Holes and cracks in the floor, loose tiles, and protruding nails are the most common causes of trip accidents. Therefore, the management should hire professionals to fix damaged parts of the floor or prevent workers from accessing these areas. If it is impossible to clean spills on time, consider investing in anti-slip flooring. First aid training ensures employees can help those who trip, slip, and fall in the workplace to minimize injuries.
Clear the Emergency Exits
Sometimes an emergency may arise in the factory, making employees run for safety. A cluttered work area and blocked exits make the work environment unsafe. A cluttered exit might prevent employees from escaping during an emergency. Therefore, mark exits clearly and ensure they are accessible at all times. Employees should always store tools and equipment in their respective storage locations after use to minimize clutter in the workplace or fire exits.
Create Shifts and Work Breaks
Fatigue is one of the leading causes of accidents in factories. Therefore, it is crucial to allow employees to work in shifts and take breaks to refresh and rejuvenate. Working long hours without a break could increase human error since employees may not observe safety measures or identify dangers in the surroundings when tired. Employees will undoubtedly feel motivated and stay alert after taking a break. The ideal number of hours per shift might vary depending on the type of work, working conditions, and availability of trained employees.
Label Chemicals Accordingly
Some chemicals look alike, even for trained eyes with years of experience. For example, an acid might look like water, and mixing it with other chemicals could lead to a hazardous reaction. Therefore, labeling chemical containers can save lives by preventing incorrect handling or disposal of hazardous chemicals. The employees should be able to access material safety data sheets and read them before using any chemicals. These sheets highlight potential hazards and safety procedures necessary when handling the chemicals.
Prevent Objects from Falling
Stored chemical containers might fall on workers or other chemicals, leading to injuries. To keep things from falling, use nets, toe rails, and toe boards, and stack chemical boxes appropriately. Remember to place heavy objects on the lower shelves and lighter ones above them. The chemicals should be stored away from the regular work areas to minimize the risk of falling.
Although it is hard to prevent all emergencies in chemical industries, these simple measures can minimize accidents. Remember to train employees and store chemicals appropriately in labeled containers. It is also crucial to consult professionals to help with safety planning, safety training, and emergency prevention and response.