Oven Calibration and Validation: Ensuring Accurate Test Conditions
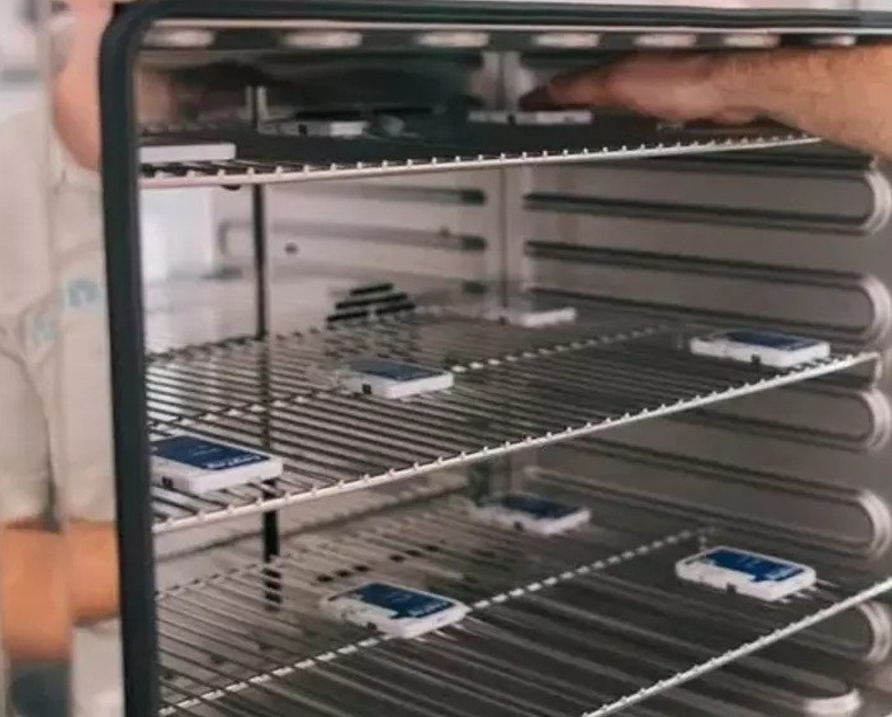
Oven Calibration and Validation: Ensuring Accurate Test Conditions
In the realm of manufacturing and industrial processes, precision and reliability are paramount. Among the vital tools that contribute to these factors are industrial ovens. These versatile appliances play a crucial role in various industries, from aerospace to electronics, by facilitating processes such as curing, drying, and heat treatment. In order to maintain consistent quality and reliable results, it is imperative to discuss a fundamental aspect of oven operation: calibration and validation. In this article, we delve into the significance of oven calibration and validation, shedding light on the importance of accurate test conditions and their impact on industrial processes.
Table of Contents
Understanding Industrial Ovens
Industrial ovens are workhorses of modern manufacturing, serving as indispensable tools in numerous applications. They are used for processes ranging from baking to curing, drying to heat treatment. The effectiveness of these ovens depends on their ability to maintain precise temperature and environmental conditions consistently. Achieving such precision requires meticulous calibration and validation.
Importance of Calibration and Validation
Calibration: Calibration refers to the process of adjusting an oven to ensure that its temperature readings match a standard reference. This is essential because over time, factors like wear and tear, fluctuations in power supply, and exposure to extreme conditions can cause an oven’s internal temperature to deviate from its setpoint. Such deviations can lead to suboptimal process outcomes, affecting product quality and efficiency.
Validation: Validation, on the other hand, involves confirming that an oven consistently performs within predetermined specifications. This process is critical in industries where even minor variations can lead to defective products or compromised safety. By validating an industrial oven, manufacturers can ensure that it reliably produces the intended results, meeting regulatory and quality standards.
Ensuring Accurate Test Conditions
Accurate test conditions are the bedrock of dependable manufacturing processes. When an oven is calibrated and validated, it operates within a tightly controlled range, enabling consistent results. This is particularly important for industries that require specific curing times, temperature profiles, and material properties. For instance, in the production of electronics, deviations in the curing process could lead to solder joint failures, impacting product functionality and longevity.
Steps in Oven Calibration and Validation
1. Temperature Mapping: The first step involves conducting a temperature mapping exercise. This entails placing temperature sensors at various locations within the oven and running it through its operating range. The resulting data helps identify temperature variations across the oven’s interior, enabling adjustments to be made.
2. Adjustment: Once temperature variations are identified, adjustments are made to the oven’s controls to ensure uniform heating. This may involve recalibrating the temperature settings or fine-tuning the heat distribution mechanisms.
3. Validation Testing: After calibration, the oven undergoes validation testing. This involves running sample processes and analyzing the results against predetermined criteria. If the oven consistently meets these criteria, it is deemed validated.
Benefits of Proper Calibration and Validation
1. Enhanced Product Quality: Accurate oven conditions lead to consistent product quality, reducing defects and rework.
2. Optimized Efficiency: A calibrated and validated oven operates at peak efficiency, minimizing energy wastage.
3. Regulatory Compliance: Many industries are subject to strict regulations. Proper calibration and validation ensure compliance with these standards.
4. Longevity of Equipment: Regular maintenance through calibration and validation extends the lifespan of industrial ovens.
Conclusion
In the intricate landscape of modern manufacturing, precision and reliability form the cornerstones of success. Industrial ovens, indispensable tools in this arena, must perform with utmost accuracy to yield consistent, high-quality results. Through meticulous calibration and validation processes, manufacturers can ensure that their ovens operate within tight specifications, paving the way for dependable production processes, regulatory compliance, and customer satisfaction. At Certified Material Testing Products, our commitment to oven calibration and validation is a testament to the industry’s dedication to excellence and innovation. We understand the critical role that certified materials play in achieving optimal performance, and our products are designed to meet the highest standards. Trust us to provide the tools you need to enhance precision, elevate reliability, and ensure success in your manufacturing endeavors.