Everything You Need to Know About A356 Aluminum
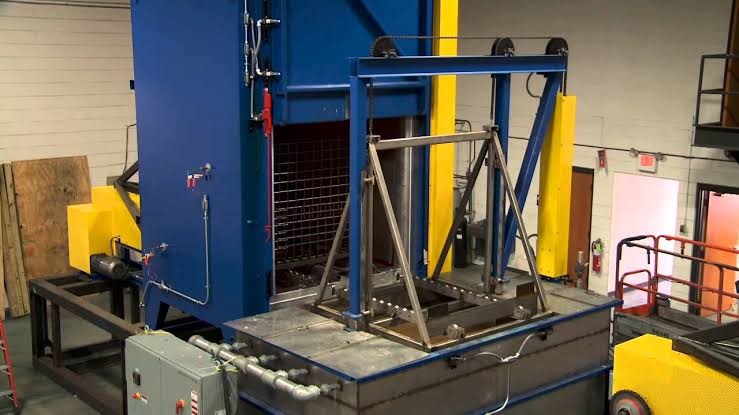
Introducing a356 aluminum, a versatile and valuable material revolutionizing industries around the world. If you have been searching for information on this remarkable alloy, look no further! We will discuss the history, applications, advantages, and production processes of A356 aluminum in this article. We will guide you through all the facts you need to know about A356 aluminum – one of the industry’s game-changers.
Table of Contents
History and Development of A356 Aluminum
The journey of A356 aluminum’s history and development spans several decades, beginning in the early 1900s when researchers aimed to enhance aluminum alloys’ strength and durability. By the 1930s, breakthroughs in alloying techniques led to the creation of A356 aluminum, composed primarily of aluminum with additions of silicon and magnesium for improved properties. Advancements in metallurgical practices over time refined A356 aluminum, resulting in a high-performance alloy suitable for casting complex shapes without compromising structural integrity.
Today, it is widely used in automotive manufacturing, aerospace engineering, and consumer electronics due to its exceptional strength-to-weight ratio, corrosion resistance, and thermal conductivity. The evolution of A356 aluminum underscores its significance in modern industry. As technology advances, we can anticipate further exciting developments for this remarkable material.
Applications and Uses of A356 Aluminum in Different Industries
This versatility is a testament to its unique combination of properties. Here’s a summary of how A356 aluminum is utilized in different sectors:
- Automotive Industry: A356 aluminum is used for manufacturing engine components, structural parts, wheels, and suspension components in the automotive sector, benefiting from its strength-to-weight ratio and corrosion resistance.
- Aerospace Industry: In the aerospace industry, A356 aluminum is important for producing aircraft structures, including fuselage panels and wings. Its high strength-to-weight ratio reduces overall weight while ensuring structural integrity.
- Marine Industry: A356 aluminum is employed in the marine industry for constructing boat hulls and other components due to its resistance to saltwater corrosion.
- Construction Industry: A356 aluminum finds applications in the construction industry, contributing to architectural structures like bridges and buildings. Its durability, ease of fabrication, and aesthetic appeal make it a valuable material.
- Electronics Industry: A356 aluminum is used in the electronics industry for producing heat sinks that dissipate excess heat generated by electronic devices, ensuring efficient thermal management.
The versatility of A356 aluminum, driven by its exceptional properties, allows it to cater to diverse needs in these industries, contributing to lightweight, durable, and corrosion-resistant components across various applications. This adaptability makes it a preferred choice for many manufacturers seeking efficient and high-performance materials.
Advantages and Disadvantages of A356 Aluminum
The advantages and disadvantages of A356 aluminum, which is valuable for those considering its use in various applications. Let’s summarize the key points:
Advantages of A356 Aluminum:
- Lightweight:
- A356 aluminum is lightweight and beneficial for applications prioritizing weight reduction.
- Contributes to increased fuel efficiency and easier handling during manufacturing processes.
- High Strength-to-Weight Ratio:
- Despite its lightweight nature, A356 aluminum boasts an excellent strength-to-weight ratio.
- Suitable for structural components in industries such as aerospace and automotive.
- Good Machinability:
- Easily machinable, allowing for efficient shaping, cutting, and forming into intricate shapes.
- Contributes to streamlined manufacturing processes and reduced production costs.
Disadvantages of A356 Aluminum:
- Poor Corrosion Resistance:
- Relatively low corrosion resistance, especially in harsh environments like saltwater or acidic conditions.
- Requires proper surface treatment or coating to enhance corrosion resistance.
- Limited Weldability:
- Challenging to weld due to the formation of shrinkage porosity during solidification.
- Specialized welding techniques may be necessary to maintain desired mechanical properties.
- High Production Costs:
- Production costs for A356 aluminum can be higher than other alloys.
- Factors include raw material costs and specialized casting processes needed to achieve desired mechanical properties.
In conclusion, A356 aluminum offers advantages like lightweight properties, a high strength-to-weight ratio, and good machinability, making it suitable for various applications. However, considerations such as poor corrosion resistance, limited weldability, and higher production costs should be carefully assessed based on specific application requirements. Manufacturers need to weigh these pros and cons to determine if A356 aluminum aligns with their needs and objectives.
Common Production Processes for A356 Aluminum Parts
The common production processes for A356 aluminum parts are essential for achieving high-quality results in various industries. Let’s summarize these key production processes:
- Casting
- Casting is a widely employed production process for A356 aluminum parts.
- It involves pouring molten A356 aluminum into a mold and allowing it to solidify into the desired shape.
- This process is preferred for its ability to create complex shapes with high precision and accuracy.
- Machining
- Machining is another prevalent production process for A356 aluminum parts.
- It utilizes tools like lathes, mills, and drills to remove excess material from a block or sheet of A356 aluminum, achieving the desired shape and dimensions.
- Machining allows for precise control over tolerances and surface finishes.
Selecting the most appropriate production process based on design specifications and application needs is pivotal to ensuring optimal performance and durability of A356 aluminum parts. This knowledge is particularly valuable for industries such as automotive, aerospace, and construction, where A356 aluminum plays a significant role in delivering high-quality components.
Maintenance and Care for A356 Aluminum Materials
Maintaining and caring for A356 aluminum materials is important for preserving their appearance, structural integrity, and performance.
- Regular Cleaning: Clean away dirt, grime, and contaminants using a mild detergent or soap mixed with water. Avoid abrasive cleaners to prevent surface damage.
- Thorough Drying: After cleaning, ensure thorough drying to prevent moisture buildup and corrosion. Use a soft cloth or towel to remove excess water.
- Protective Coating: Enhance longevity by applying a protective coating such as anodizing or painting. This creates a barrier against oxidation and corrosion.
- Regular Inspections: Identify signs of wear or damage early on through regular inspections. Check for cracks, dents, or areas where protective coatings may have worn off. Prompt repairs can prevent further deterioration.
- Proper Storage: Store A356 aluminum materials in a clean and dry environment when not in use. Avoid exposure to extreme temperatures or humidity, as these conditions can accelerate degradation.
By incorporating these maintenance practices into your routine, you can ensure that your A356 aluminum materials not only remain visually appealing but also maintain their structural integrity and performance over an extended period.
Future Trends and Innovations in the Use of A356 Aluminum
The ongoing advancements and trends in utilizing A356 aluminum are fascinating and hold significant potential across multiple industries. Here’s a recap:
- Additive Manufacturing (3D Printing): Researchers are exploring the use of A356 aluminum powder in additive manufacturing, allowing for the creation of complex parts with intricate designs. This represents a cutting-edge approach to production.
- Integration in Lightweight Vehicles: A356 aluminum is gaining traction in the automotive industry for lightweight vehicle components. Its ability to reduce weight while maintaining strength aligns with the industry’s focus on fuel efficiency and emissions reduction, contributing to improved performance and sustainability.
- Aerospace Applications: A356 aluminum is increasingly considered for aircraft structures in the aerospace sector. Its high strength-to-weight ratio makes it an ideal choice for durable yet lightweight components, potentially leading to more fuel-efficient aircraft designs.
- Surface Treatment Advancements: Ongoing developments in surface treatment technologies aim to enhance the corrosion resistance and wear properties of A356 aluminum parts, extending their lifespan and expanding applications.
In conclusion, the future holds exciting possibilities for A356 aluminum, and ongoing research and development efforts are shaping a more efficient and eco-friendly industrial landscape across various sectors.
Conclusion: Why A356 Aluminum is a Valuable Material in Today’s Industry
Overall, A356 Aluminum stands out as a multifaceted and extensively utilized material in various sectors due to its impressive attributes including a favorable strength-to-weight ratio, exceptional castability, and resistance to corrosion. Although obstacles like expense and low melting point may be present, its ability to be recycled promotes efforts toward sustainability. The incorporation of various production methods also aids in effective production, with continuous research aimed at improving its characteristics. Given the A356 Aluminum’s versatility and worth, it is poised to play an important role in propelling future industrial developments.