Investigating the Causes and Mitigation Strategies for PCB Warping in Electronic Devices
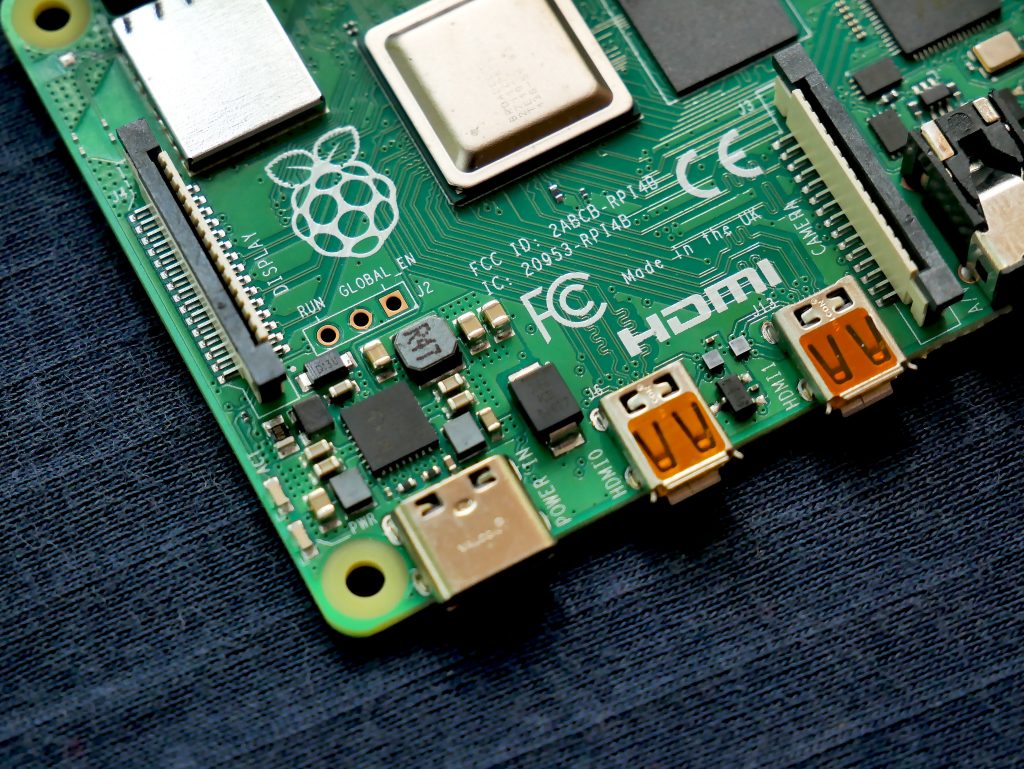
Printed circuit boards (PCBs) are crucial components in electronic devices, providing the foundation for electrical connections and component integration. However, PCB warping can occur during manufacturing or throughout the device’s lifespan, leading to performance issues and potential failure. In this article, we will explore the causes of PCB warping and discuss effective mitigation strategies. By understanding these causes and implementing appropriate measures, engineers and manufacturers can ensure the optimal functionality, reliability, and longevity of electronic devices.
Table of Contents
Understanding PCB Warping
Definition of PCB Warping: PCB warping refers to the deformation or distortion of a PCB from its original flat and planar state. It can manifest as bowing, twisting, or flexing, negatively impacting the board’s structural integrity and performance.
Effects of PCB Warping on Device Functionality: PCB warping can lead to several adverse effects on device functionality, including mechanical stress on components, disrupted electrical connections, signal integrity issues, thermal management challenges, and mechanical interference.
Common Locations of Warping in PCBs: Certain areas of a PCB are more prone to warping, such as regions with high component density and the board’s edges and corners.
Importance of Addressing PCB Warping Issues: Addressing PCB warping is crucial to ensure device reliability, performance, and longevity. Failure to address warping can result in system malfunction, increased costs, and reputational damage.
Causes of PCB Warping
Temperature Variations and Thermal Stress: Temperature fluctuations during manufacturing and operation can cause thermal stress, leading to warping. Factors contributing to temperature-related warping include uneven heating and cooling during soldering and thermal cycling during device operation.
Improper Material Selection and Coefficient of Thermal Expansion (CTE): Mismatched CTEs between layers and components can induce stress and warping. Optimal material selection and considering the CTEs of different materials are crucial to minimize stress differentials. The choice of substrate material also affects warping.
Inadequate PCB Thickness and Mechanical Stability: Thin PCBs lack structural rigidity and are prone to warping. Factors related to inadequate thickness include the impact on warping, considerations for appropriate thickness, and effects during soldering.
Incorrect Storage Conditions: Improper storage conditions, such as high humidity levels and temperature fluctuations, can contribute to warping over time.
Manufacturing Process Deficiencies: Deficiencies in the manufacturing process, such as inadequate handling, improper alignment, excessive mechanical pressure during assembly, inadequate curing of the solder mask, improper lamination techniques, and inadequate cooling after soldering, can lead to warping.
Mitigation Strategies for PCB Warping
Design Considerations for Warping Mitigation: Proper PCB design plays a crucial role in mitigating warping. Considerations include optimizing component placement, minimizing thermal stress, balancing copper distribution, and incorporating features like stiffeners and support structures.
Material Selection and CTE Management: Careful material selection, ensuring matched CTEs between layers and components, and using substrates with appropriate thermal properties contribute to warping mitigation.
PCB Thickness and Mechanical Stability: Choosing an appropriate PCB thickness based on component size, weight, mechanical requirements, and considering the mechanical stress during handling and assembly help prevent warping.
Thermal Management: Effective thermal management techniques, such as proper heat sink placement, optimized copper traces for heat dissipation, and thermal vias, help maintain uniform temperature distribution.